Desiccants, Desiccators, Oxygen Absorbers and Other Moisture Control Solutions
AGM moisture control products are designed to protect the contents of sealed containers from the harmful effects of moisture or oxygen.
- Container Access
- Corrosion Prevention
- Humidity Monitoring
- Moisture Control
- Moisture Purging
- Pressure Control
- Shelving & Straps
- Shock Monitoring
Find What You're Looking For
It’s a lot, we know. If you’re looking for something specific or aren’t sure what you need, try searching through all products or give us a shout and we’ll help!
AGM Moisture Control Products
AGM designs, manufactures, and distributes desiccants and desiccator products to a wide variety of industries. These desiccants are available in bulk, bagged, and custom made options.
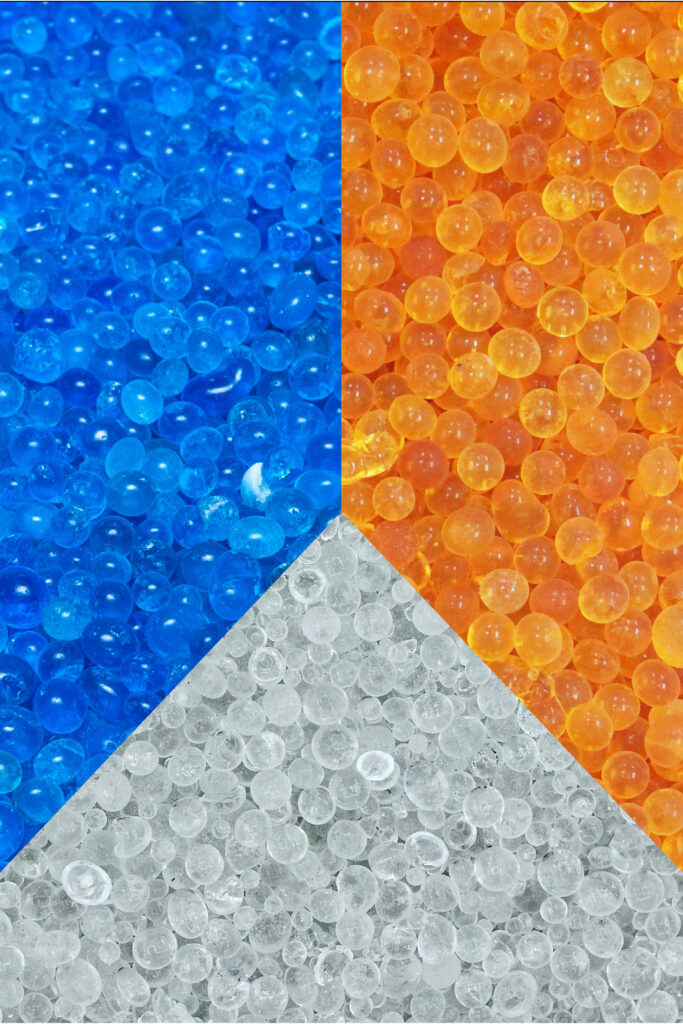
Why is it important to control moisture in a sealed container or enclosure?
Moisture in a sealed space can result in rust, corrosion, short-circuiting, fogging, or soaking of components. As a result, component functionality may be decreased or stopped, goods may be ruined, or operational lifespans diminished. Essentially, trapped moisture can wreak havoc on the internals of an item or the cargo of a container. Therefore, maintaining appropriate dryness levels within an enclosure is necessary for the successful operation of any item and safe transport of equipment.
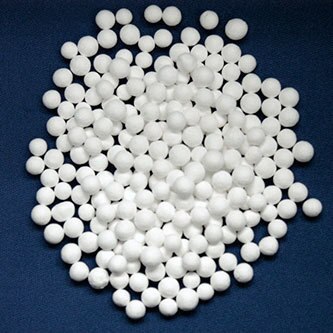
Bulk Desiccants
Silica gel, molecular sieve, activated alumina – AGM provides all of these desiccants in bulk quantities.
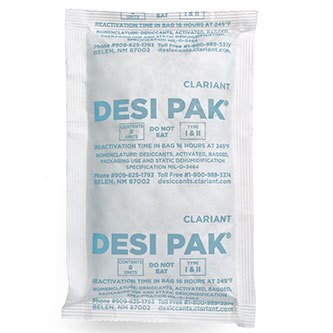
Bagged or Packaged Desiccants
AGM bagged or packaged desiccants provide an easy and contained method of desiccation. These desiccants are generally packaged in bags, packets, or canisters. Packets are sometimes referred to as “sachets” or “pouches.”
Bagged desiccants are available in:
• Tyvek® (heat sealed)
• Kraft paper (heat sealed)
• Heavy, non-woven rayon/polyester blend (string sewn)
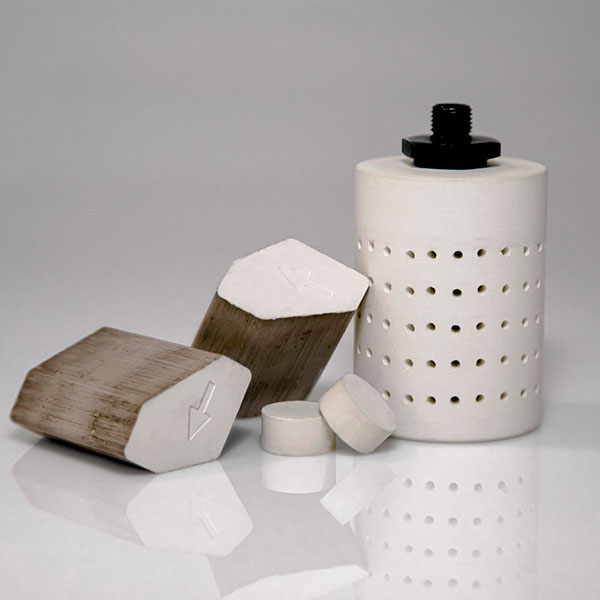
AGM H2OLock Custom Pressed Desiccant
H2OLock is AGM’s pressed desiccant. Made from a combination of molecular sieve and proprietary binders, this pressed desiccant is capable of moisture adsorption and capacity greater than other comparable desiccants. Further, it may be shaped and formed to customer specifics, in addition to standard shapes.
H2OLock Custom Pressed Desiccants
Custom pressed desiccants may be shaped and formed to customer requirements, are strong enough for use as structural components, and can feature adsorption rates and capacity greater than comparable desiccants.
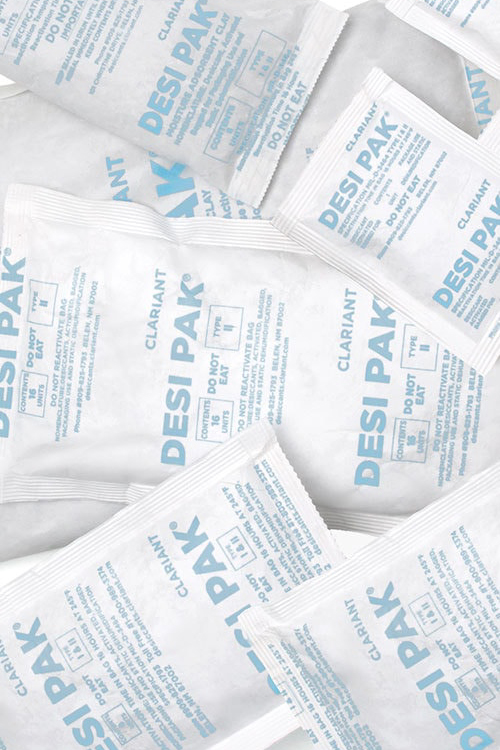
How to select the right moisture control solution for your product?
Typically, a moisture solution involves either desiccants, desiccators, oxygen absorbers, dry-gas purging – or some combination thereof.
Which solution is right for you and your project is dependent upon several factors, including:
- The desired operational lifespan of the equipment
- The equipment’s sensitivity to moisture
- The equipment’s planned storage and operational environments
- The types of seals used on the container and the container material itself.
There are other considerations as well, making a determination that will properly safeguard your equipment something that isn’t one size fits all. That’s why we highly recommend reaching out to AGM and discussing your project with our engineering team.
For more information or help on what type of moisture control solution you need, get in touch with us.
Industry Applications
Some common industry applications for our moisture control solutions include:
- Aerospace: Our desiccators and nitrogen purging systems help protect rocket engines.
- Defense: Use desiccant for everything from storing equipment and munitions to installing it in cameras and missiles.
- Shipping & Logistics: Use large desiccant sacks to help reduce moisture damage in shipping large quantities of cargo in large containers.
- Electric Vehicles: Use custom desiccants to protect battery cases.
AGM offers custom engineering services so you can get exactly what you need.
FAQs
Yes, condensation can occur inside of a sealed container. For more information on how condensation occurs and ways to prevent it from happening, visit our blog
There are four ways for water vapor or liquid water to enter a sealed enclosure:
1. Water Vapor In The Air Inside The Package
Water vapor in the air can be trapped inside an enclosure during sealing. Depending on the project and the components involved, it isn’t always possible or cost-effective to dry-gas purge, and construction inside a dry room is not always available or a guarantee. for this reason, desiccants are commonly used to absorb moisture from the enclosed space.
An easy example is found in pharmaceuticals, where desiccants and oxygen absorbers are included inside pill bottles to adsorb moisture trapped inside when the bottle is sealed, as well as moisture that enters during repeated openings.
2. Moisture Contained In The Materials Inside The Package
The materials used in many complex constructions, especially within the aerospace, military and space industries, are themselves constructed under specific conditions. For example, circuit boards are commonly constructed in approximately 70% relative humidity conditions. As a result, circuit boards absorb moisture.
To prevent off-gassing, many enclosures are purged with dry gas, such as nitrogen, when sealed, in an effort to push out all water vapor. However, dry-gas purging requires flowing gas through an enclosure and can take quite a while to fully accomplish the desired result. Some of our customers have related their own experiences with dry-gas purging their projects only to find humidity or condensation and water inside the project enclosure later on.
A desiccant can be used in order to adsorb the off-gassed moisture. In these situations, however, it is important to consider desiccant adsorption rates, desiccant equilibrium points, and desiccant discharge rates.
3. Moisture In Or On The Walls Of The Package
All materials have a permeability rate, although different materials have different permeation rates.
Moisture Vapor Transmission Rate (MVTR), is a measurement of how quickly moisture vapor will diffuse through a material. In our case, the packing and walls of sealed enclosures. These rates can be quite slow, while others can be fast (e.g. tinfoil and fabric). Factors affecting MVTR include temperature and humidity throughout the course of the enclosure’s life. In a sealed enclosure, water vapor will push through packaging in order to equalize pressure. Furthermore, moisture ingress will occur should an enclosure wall develop even a small hole.
The go-to solution for mitigating this issue is desiccant, either bulk or custom. Additionally, humidity indicator cards are often installed in the enclosure to help track internal humidity levels and manage accurate desiccant change-outs.
4. Moisture Entry Into The Package Due To Permeation Or Leakage
Similar to component off-gassing, the walls of an enclosure or packing material may contain moisture. For example, a container constructed in an open environment most likely is not thoroughly dry when finished.
Again, dry-gas purging is not necessarily always feasible due to the enclosure size, construction, or cost. In these scenarios, it’s easier and more cost-effective to employ either bulk or custom desiccant.
Find What You're Looking For
It’s a lot, we know. If you’re looking for something specific or aren’t sure what you need, try searching through all products or give us a shout and we’ll help!