Sealed Environment Maintenance and Moisture Analysis
Hydra₂O™ Moisture Analysis is an analytical service that helps you predict the long-term moisture ingress into your sealed enclosure or space, and prescribes precise desiccant requirements and seal recommendations to prevent moisture damage.
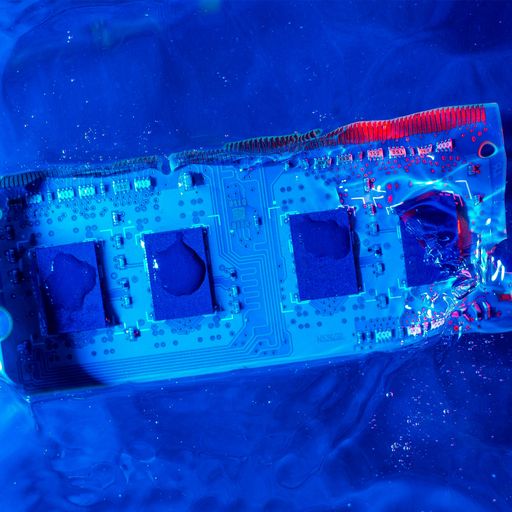
What is Hydra20 Moisture Analysis?
Hydra20 is a moisture analysis tool specifically for use in predicting the ingress of moisture into a sealed space over time.
Unlike other moisture analysis services that measure the level of moisture in solids, liquids, and gasses, Hydra20 is designed for use by engineers in technical industries to determine moisture protection processes and products to protect their equipment from moisture damage.
If your project requires precise moisture level maintenance throughout its lifespan, contact us for a custom desiccant solution!
What’s Included: Our Hydra₂O™ Moisture Analysis Service
Our Hydra₂O™ Moisture Analysis is essentially a very comprehensive calculator used to predict long-term moisture ingress for your sealed enclosure and prescribe precise desiccant requirements to protect it.
You will be provided with a precise amount of desiccant needed to protect your enclosure for a specified amount of time and input parameters. The Hydra₂O™ Moisture Analysis Tool can adjust these parameters (e.g. seal materials, etc), in up to three “Runs” for the specific enclosure to find out what will best help you achieve the most effective combination.
Unlike standard packing specifications that cannot specify moisture requirements beyond the general parameters (such as MIL-STD-2073-1), the Hydra₂O™ Moisture Analysis Tool takes into account the different variables that are important to each unique situation, such as the:
- Estimate of moisture held by materials inside the enclosure when it is sealed
- Information about the materials inside of the enclosure
- Moisture in hygroscopic materials
- Target dryness level and length of time moisture protection is required
- Container wall permeability
- Material and geometry of any non-metallic enclosure walls
- Seal types, materials, cross-section geometry, and length
- Leak down test data (starting and ending pressure, time, gas medium)
- Environmental exposure conditions
- Environmental conditions under which the enclosure is sealed if not dry gas purged
- Length of time over which protection is required
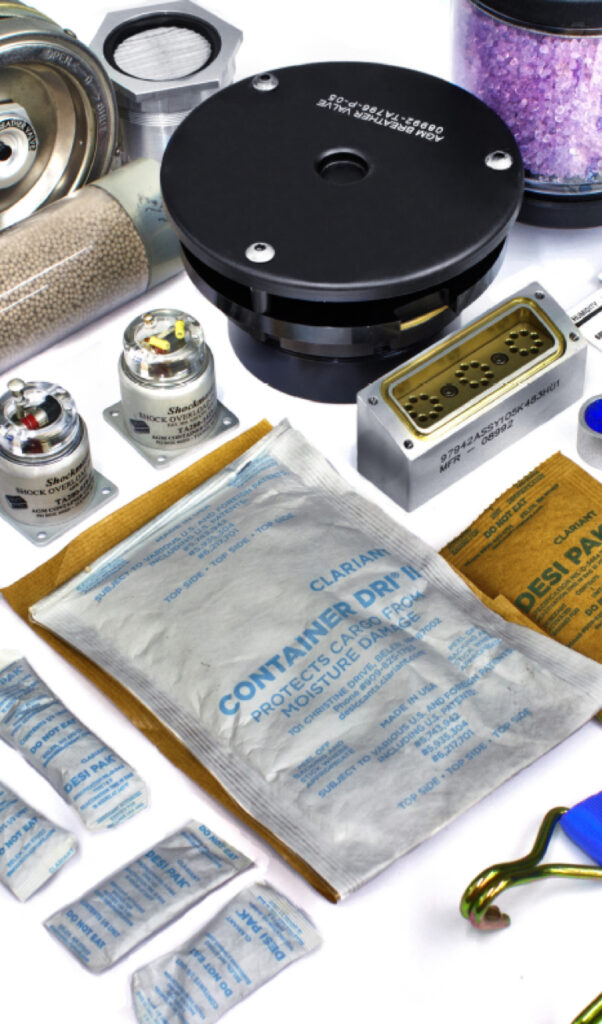
How to Get Started with Hydra₂O™
How to Get Started with Hydra₂O™
- If you’re in need of a custom solution for moisture control, you can get started by contacting our engineers who will gather the required information from you for use with our Hydra tool (see information list below).
- Once our engineers gather the information needed they will input that data into our Hydra₂O™ tool.
- AGM Engineers will use the data and calculations from Hydra20 to find and provide solutions. This information will be shared with you over an email or phone call (with an accompanying email of the results). This is usually a jumping-off point for our engineers to work with you in setting you up with the right custom desiccant solution.
Do you have a difficult moisture problem? Contact our sales department about putting Hydra₂O™ to work for you.
What We Need From You
Our engineers will request the following information from you to ensure our tool can provide the right solution:
- Target dryness level and length of time over which protection is required
- External conditions (AR 70-38 Hot-Humid or Variable High Humidity are default options)
- Enclosure air volume
- Seal materials, cross-section geometry, and length
- Material and geometry of any non-metallic enclosure wall
- Environmental conditions under which enclosure is sealed before being put into service if an enclosure is not dry gas purged
- Leak down test data (starting and ending pressure, time, gas medium)
- Estimate of moisture held by materials inside the enclosure when it is sealed up; if this information is not available, then information about the materials inside the enclosure
Do you have the information above ready for our engineers? Contact us today to get started!
**AGM can perform a Hydra₂O™ analysis without all of the information in this list; however, the results may lose accuracy. In many cases, AGM can estimate some missing factors or uncertainty due to a lack of information. Additionally, AGM has an extensive materials library that can make up for some lack of specific knowledge. AGM will execute a non-disclosure agreement (NDA) if required for sharing of information.
Benefits Of Using Our Hydra₂O™ Moisture Analysis Tools
Our Hydra₂O™ Moisture Analysis Tool provides several extra benefits that cannot be found elsewhere including:
- Predicts long-term desiccant requirements for sealed enclosures
- Quickly analyzes the effects of different materials and sealing techniques on the life of an enclosure
- Reduces the risk of product failure
- Maximizes opportunities to reduce enclosure costs
- Reduces long-term maintenance and service costs
- Reduced cost and time risk associated with product performance testing
- Reduced design risk associated with uncertainty in input parameters
- Takes into account more critical factors for measuring and managing moisture control than standard package requirements
Ready to get started?
Find the best moisture control solution for your sealed enclosure with our Hydra₂O™ Moisture Analysis Tool.
FAQs
Yes, because our Hydra₂O™ Moisture Analysis Tool Hydra2O’s calculations take a wide array of factors into account in order to generate the most accurate prediction of enclosure performance possible.
Standard packaging specifications such as MIL-STD-2073-1 and IPC/JEDEC J-STD-033 provide guidance on protecting moisture-sensitive materials over the short term and for specific applications. For example, the military packaging specification MIL-STD-2073-1 recommends 1.2 units of desiccant per cubic foot of air volume for metal containers, with a few refinements to account for dunnage.
Standard packaging specifications like MIL-STD-2073-1 have proven themselves over time to be good enough for specific applications. That said, these standard specifications tend to be “blunt instruments”: they’re typically meant to be used only for short-term shipping and storage (usually one year or less), and they recommend a conservative amount of desiccant in order to make up for unknowns in the packaging or in the exposure conditions.
Unfortunately, moisture protection over the long term and for non-standard applications can be a complicated and difficult problem — too difficult for a standard specification to address fully. Errors in basic assumptions can compound over time and become dangerous in the long term. Extrapolating a short-term desiccant recommendation for a long-term scenario may lead to inadequate protection if an enclosure is more permeable or leaky than the “specification enclosure”.
On the opposite side of the coin, the simplified assumptions behind a standard packaging specification can also lead to the over-use of desiccants. For instance, what can be done for an enclosure that is extremely well sealed, and that doesn’t have enough space for the full standard desiccant recommendation? How well do the enclosure seals really need to be, and can their design be modified to improve their long-term performance? Therefore, standard packaging specifications provide inadequate guidance for addressing these questions.
Yes, Hydra₂O™ can predict the moisture levels in an assembly for years into the future, so one can aim for — and hit — a target dryness level. This is because Hydra₂O™ accounts for all of the factors that affect dryness levels.
For instance, the moisture-holding capacity of desiccant varies with temperature and dryness level — as shown on the standard desiccant isotherm chart below. This information is far too complex to be taken into account with a standard packaging specification, or even hand calculations, but desiccant isotherms are included in Hydra2O’s calculations.
Different types of applications require different dryness levels. For instance, electronic assemblies typically need to limit the moisture content to no more than 5000 parts per million (ppm) in order to prevent corrosion and short circuits, but optical assemblies must hold the frost point below the lowest operating temperature so that lenses and mirrors don’t fog. A frost point requirement of -40°C, which is not unusual for an optical assembly in an aerospace application, equates to a moisture content of only 125 ppm. This is 40 times drier than the typical electronic requirement.
Therefore, a standard packaging specification like MIL-STD-2073-1 can’t provide guidance on specific dryness levels because it doesn’t even acknowledge that different targets exist. And, if a product doesn’t fit the situation for which a specification was written, the specification’s desiccant recommendation may be useless, or, even worse, dangerous.
Hydra₂O™’s flexible inputs mean that it can quickly analyze the effects of materials and sealing techniques on the life of an enclosure. Will the humidity level inside a container goes out of bounds during the fourth, fifth, or even tenth year of storage? Can the cost of an optical assembly’s housing be reduced by switching to an alternate seal material? Since Hydra₂O™ accounts for all critical factors, including seal materials, the designer can reduce the risk of product failure while at the same time exploring opportunities to reduce costs.
Hydra₂O™ can reduce long-term maintenance and service costs since it can predict a container’s desiccant life with a high level of confidence, it is possible to maximize the time interval between desiccant change-outs while being confident that the enclosure contents will not be put at risk. The designer can also explore the tradeoff between the additional upfront costs of premium seals versus the long-term savings associated with reduced product maintenance.
In today’s world of ever shorter product development cycles, cutting product testing times can mean the difference between a product being the first-to-market or being a “me-too” product. Unfortunately, testing for moisture ingress can be a time-consuming process because it takes a long time for the moisture to work its way into a well-sealed enclosure. Therefore, Hydra₂O™can reduce product test time because it provides the correct data for getting the design right the first time around — no repeat product testing is required!
Hydra2O can quickly determine the effects of parameter variability on the performance of an enclosure and put a boundary on their effects. For example, perhaps the exact conditions in which the product will be used or stored are unknown, or there is some uncertainty in the permeability of one of the enclosure’s seals. Perhaps the uncertainty really isn’t that important — or maybe it’s critical! Either way, the designer can focus on the aspects of the enclosure design that really matter once the criticality of each parameter is known