WHAT ARE DESICCANTS?
Desiccants are hygroscopic materials that adsorb moisture from the air. They are often placed in packets made of kraft paper bags, Tyvek®, or custom-shaped and sewn bags. However, desiccants are also used in more advanced devices, such as in desiccators and breathing desiccators to dry an air or gas stream. Most manufactured desiccants look like small beads or caviar.
Desiccants are often used to create and maintain dry spaces, like the housing of an aerial camera, the inside of a shipping container or even a shoebox. In technical industries like aerospace, desiccant is used to protect electronics from corrosion and short circuiting, prevent sensor malfunctions, and stop fog or mold from forming on lenses. Some power generation plants use desiccants to dry gas streams and protect combustion engines from rust and volatile organic compounds (VoCs), such as siloxanes. On the other hand, residential or everyday applications of desiccant may include protecting stored photographs, books or albums.
Generally, keeping spaces dry prevents condensation, maintains low humidity levels. For these reasons, desiccant is used throughout many different industries to protect against moisture damage.
There are two main categories of desiccants: manufactured and natural. Manufactured desiccants include montmorillonite clay, silica gel, activated alumina, or molecular sieve, as well as many others. These are materials created in a lab to enhance their moisture adsorption and retention abilities. Naturally occurring desiccants include items such as salt and rice. However, silica gel is possibly the most common desiccant used in commercial, industrial, and technology industries.
Some desiccants, such as orange or blue silica gel, change color when saturated. This feature helps in knowing when to change out desiccant loads.
WHY ARE DESICCANTS USED?
The job of any desiccant is to adsorb and trap moisture. The ultimate goal of desiccant is to stop moisture from causing rust, mold, corrosion, fogging, or any other moisture related damage.
In technical industries, this means preventing corrosion from causing short circuits in commercial grade electronics as well as military or space technologies.
The food industry will use desiccants or oxygen absorbers (which are not technically desiccants) in packaging to prevent moisture from ruining sundries during shipping.
The pharmaceutical industry will include desiccants – usually oxygen absorbers but sometimes small silica gel packets – in some medicine bottles to inhibit mold growth and preserve medicines.
Additionally, desiccants and oxygen absorbers have many uses around the home. For example, oxygen absorbers may be used to increase the shelf life of many dry goods. Desiccants may be used to protect stored items in boxes or containers, such as books, records, or photographs. Further, placing a desiccant packet or two into a gun case or cabinet will prevent rust from forming on firearms and ruining ammunition, which is a significant safety concern. Such cases are especially helpful for those living in humid environments or with homes featuring swamp coolers.
CAUTION: Some desiccants are toxic; for example, blue indicating silica gel. While silica gel itself is non-toxic, the cobalt chloride – used in blue indicating silica gel – is toxic. The cobalt chloride provides a visual indication of desiccant saturation-level via color change. Nevertheless, blue indicating desiccant should not be ingested or used to preserve foods.
For more about desiccants, see the info on the Desiccants, Desiccators, and Desiccant Breathers product pages, along with FAQs and more. If you have a specific question, contact AGM!
AGM’S DESICCANT GUIDES
DO DESICCANTS EXPIRE?
Desiccants neither expire nor break down over time. Rather, desiccants adsorb moisture from the air until they cannot hold any more.
If saturated desiccants are sufficiently heated for appropriate periods of time, they will release any held moisture and again resume adsorbing. That said, swelling, cracking, and reduced performance are all possible or eventual side effects of regenerating desiccant. The heat threshold varies with desiccant type, as does the time interval for heating, and both are very easy to accidentally overdo. For these reasons, and in combination with the low price of desiccants, it’s often the choice of most to merely discard saturated desiccant. This is the case for many industrial applications as well as residential.
That said, AGM does offer a desiccant reactivator unit for silica gel desiccants.
Indicating desiccants, such as orange and blue silica gel, will change color as they saturate. In this way, it’s possible to judge whether a desiccant load needs changing or if it is still useful.
CAUTION: If there are any hazardous chemicals adsorbed in the desiccant, it can be illegal to simply throw the desiccant away. Contact personnel at your local disposal facility for information.
If using non-indicating desiccant, consider using a humidity indicator card to easily monitor humidity levels.
DESICCANT SHELF LIFE
Desiccant shelf life, especially in technical industries, is a key concern of engineers.
It’s common for desiccant to be purchased in bulk and shelved for use over a long period of time. This method of purchasing usually comes with quantity price breaks and ensures that desiccant products are on-hand when they’re needed.
However, as a material that automatically pulls moisture from ambient air, desiccants don’t last forever. That’s why desiccants are bagged and packed in sealed poly bags and metal or plastic containers. These materials prevent exposure to ambient air and feature low moisture vapor transmission rates (MVTRs) to stop desiccants from saturating prematurely.
In addition to packaging, maintaining proper storage conditions is key to ensuring a long desiccant shelf life and knowing that desiccants are ready when they’re needed.
What is the average shelf life of desiccants in their packaging?
1-year.
AGM provides a shelf-life warranty of up to 1-year, provided that recommended storage conditions are met and maintained, and that packaging is not open or damaged. However, desiccant shelf life can be adjusted to accommodate greater durations if needed.
Contact AGM Engineers for further information
What are optimal storage conditions to achieve 1-year desiccant shelf life?
0° – 90°F (-17°C – 32°C) at 0% – 75% Relative Humidity (RH)
AGM recommends a storage environment between 0° – 90°F and 0% – 75% relative humidity. In this environment, standard packaging should provide a desiccant shelf life of up to 1-year or more.
What is the standard packaging used to achieve a 1-year shelf life?
Bulk desiccant products are often shipped in unsealed poly bags inside of either metal cans or plastic pails. These materials feature low MVTRs in comparison to many other materials and play a significant role in a desiccant’s shelf life.
Similar to bulk desiccants, assembled desiccator products are sealed in partially-evacuated barrier bags and overpacked into either metal cans or plastic pails. Additionally, sacrificial desiccant – extra desiccant included to compensate for an expected level of saturation before use – may be included, depending on the product, desired shelf life and storage conditions.
Remember, desiccants adsorb moisture automatically, meaning that any time they are exposed to ambient air, they will begin collecting water vapor. For this reason, it is important that desiccants remain in their packaging until it is time to use them.
Do recommended storage conditions differ with desiccant type or amount?
Largely no. Storage conditions remain the same for all desiccants that AGM markets. However, there is potential to expand the temperature range for molecular sieve. Nevertheless, the standard range is preferable, even for molecular sieve, unless necessary.
How to achieve 1-year desiccant shelf life under non-optimal storage conditions?
The recommended storage environment range covers most locations and situations; however, there are always exceptions.
One common example is storage at elevated temperature (greater than 90°F). An elevated storage temperature may drive greater need for selecting between desiccant types. In this case, molecular sieve may be a preferred choice due to its performance at higher temperatures in comparison to clay or silica gel. However, each situation is unique and so needs case-by-case evaluation to determine the best alternative. Otherwise, desiccants may saturate or ruin before they’re used.
For Analysis On Achieving A Target Shelf Life Contact AGM Engineering.
Is it possible to extend the operational life of desiccants?
The operational lifespan of a desiccant is dependent upon usage conditions and there is little to be done to offset desiccant saturation here.
During storage, desiccant life may be extended through improvements to a container’s seals or the desiccant packaging. However, in operational conditions, the environment is not always so controlled. For example, in air flight scenarios, pressure equalization for an enclosure may be necessary to protect it and its internal components from unsafe pressure differentials. To do so, it’s common to install breather valves or breathing desiccators. However, moisture ingress occurs when the breathers open to relieve pressure, and the desiccant is there to adsorb this moisture.
Under these and similar conditions, extending the operational life of a desiccant load to a significant extent is normally not possible.
What is there to know when determining operational life?
A close analysis of environmental conditions on the ground as well as of those needed inside of the device or enclosure in question is necessary. This analysis includes temperature range, humidity levels, pressure deltas, and others.
Sometimes it’s necessary to extend this analysis to varying elevations. For example, in the aerospace industry, it’s common for aerial mounted devices to require breathing desiccators. These breathing desiccators combine breather valves with desiccant cartridges to protect the device from dangerous pressure differentials as well as moisture ingress that occurs when the breather opens. In these and other cases, calculations are performed to analyze environmental and pressure conditions at altitude, which in turn provide estimations of desiccant operational lifespan.
Determining desiccant shelf life and operational lifespan is crucial to the successful operation of just about any hardware. However, the issue goes beyond “how much desiccant do I need.”
While quantity does play a significant role; packaging, storage conditions, housing when in use, and frequency of exposure to ambient air are all of important variables as well. Without accounting for each properly, condensation can damage or ruin valuable electronics and optics assemblies, crash planes, or destroy trade goods.
Understand How Long Your Desiccant Will Last
How Much Desiccant is Enough?
Quantities of desiccant are measured in units. One unit of desiccant is defined in MIL-D-3464E as “the amount of desiccant that will absorb at least 3.0g of water vapor at 20% relative humidity and at least 6.0g of water vapor at 40% relative humidity at 77°F (25°C).”
Such a definition means that the quantity of one unit of desiccant changes with each type. However, as a general best practice, it is recommended to use 1.2 units of desiccant per cubic foot of air volume.
To help make quick estimates, AGM’s Desiccant Calculator provides unit quantity amounts based on an internal volume measurement. The tool is free to use and provides unit estimates for three common desiccants: Silica Gel, Molecular Sieve, and Clay.
If your project requires specific attention, contact AGM for greater analysis.
HOW TO CHOOSE A DESICCANT
For most applications, such as those around the house, a few packets of silica gel will do the job. For the more ambitious, the general MIL-SPEC calculation and calculator will suffice just fine. For the professional, however, it can be a little more complicated.
Start with the following checklist:
- What is it that you want to protect?
- What is the volume of interior space to be protected?
- Of what material(s) do the outer/inner/packing consist?
- What is the amount and shape of space available to install desiccant or desiccators?
- How is the container/enclosure/package sealed?
- What is the level of moisture protection required?
- What is the ambient moisture and temperature level?
- What is the length of time desired before changing out desiccant loads?
- What is the anticipated leakage rate of the enclosure?
- Is a breather valve and/or humidity indicator required?
- Is dusting protection required?
- Is RFI/EMI protection required?
- Are any unusual environmental conditions present or anticipated?
- Any additional questions or desires
Once the above questions have been answered (or even if there are few unknowns), you’ll need to contact AGM. AGM Engineering will work with you to find and provide either an off the shelf or a custom solution that ensures the safety and longevity of your project.
COMPARE ADSORPTIVE ABILITIES OF DESICCANTS
Start by comparing the properties and capabilities of different desiccants. Pay close attention to project goals and needs as choosing an appropriate desiccant is determined by them. For more detailed information about desiccant adsorption and capacity rates, contact AGM.
Figures 1 and Figure 2 illustrate the adsorption rates (how quickly water vapor is adsorbed) and the adsorption capacities (how much water vapor is adsorbed to reach equilibrium at various relative humidity readings) of silica gel, clay, and molecular sieve (synthetic zeolite) desiccants.
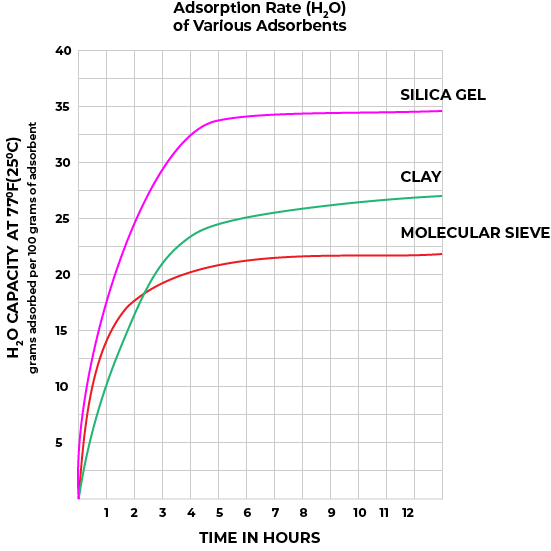
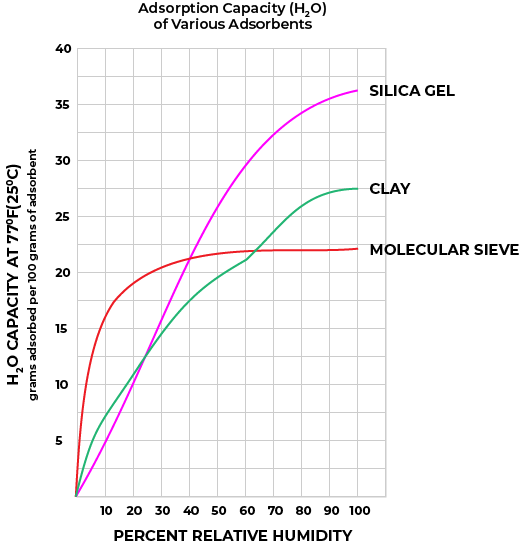
Figure 1
Figure 2
Custom Desiccants
Pressed Desiccants
Pressed desiccants are typically used when space is limited, or the desiccant’s shape is important. This type of desiccant is often machinable and thereby may be made to conform to complex and custom shapes in a range of sizes.
Furthermore, on a per volume basis, pressed desiccants often feature a greater adsorption capacity in comparison to traditional bagged or beaded desiccants. Finally, because pressed desiccants are solid, they may be secured in place using adhesives, screws, or some other fastening method.
Molded Desiccants
The benefit of using molded desiccants is found in their form factor and size. The desiccant is shaped using injection molding techniques to create a shaped desiccant that can occupy up to 100% of the the available space, if desired. Furthermore, the material combination is such that the resulting desiccants are strong enough for use as structural components in the design. As a manufacturing process, injection molding enables quantity order at lower costs.
Injection molded desiccants are commonly made from a combination of some desiccant, nylon binder, and various other proprietary additives. This combination of materials delivers optimized adsorption, strength, and form capabilities to best meet customer needs.
SOME COMMON DESICCANTS
Silica Gel (SIO2 * H2O)
Perhaps the most commonly used desiccant, silica gel, is an amorphous form of silica manufactured from sodium silicate and sulfuric acid. Its interconnected pore structure forms a vast surface area that will attract and hold water by adsorption and capillary condensation, allowing silica gel to adsorb about 40% of its weight in water. Silica gel is extremely efficient at temperatures below 77°F (25°C) (see Figure 1 and Figure 2 above), but will lose its adsorption capacity as temperatures begin to rise, much like clay (Table 2). Much of silica gel’s popularity is due to its noncorrosive and non-toxic nature; some grades have received U.S. government approval for use in food and drug packaging.
Molecular Sieve (Synthetic Zeolite, also known as Aluminosilicate)
Molecular sieve contains a uniform network of crystalline pores and empty adsorption cavities, which give it an internal adsorptive surface area of 700 to 800 m^2. Because of its uniform structure, molecular sieve will not desorb moisture into the package as readily as silica gel or clay as temperatures rise. Being synthetic rather than naturally occurring, molecular sieve is higher in cost per unit, but due to its extremely large range of adsorptive capabilities, it is often be the best value.
Montmorillonite Clay
Montmorillonite clay is a naturally occurring adsorbent created by the controlled drying of magnesium aluminum silicate of the sub bentonite type. This clay will successfully regenerate for repeated use at very low temperatures without substantial deterioration or swelling. However, this property causes clay desiccant to desorb moisture readily back into the container as temperatures rise. Clay is inexpensive and highly effective within normal temperature and relative humidity ranges.
Activated Alumina
Activated alumina excels at drying gases; such as compressed air and natural gas. However, it is often used to filter impurities from liquids, such as in water purifiers, oil transformers, and refrigerants. Activated alumina is manufactured from synthetically produced aluminum oxide (Al2O3), which provides the desiccant with a highly porous, large surface area greater than 300 m^2/g. Additionally, activated alumina may be regenerated for extended use in some scenarios.
DESICCANT PACKAGING
Cover Stock: An important factor in the efficiency of any desiccant is the bag material (cover stock). The cover stock must allow the desiccant to do its job without harming the product. This means maintaining an acceptable adsorption rate and conforming to the product’s dusting requirements.
One common cover stock is a spunbonded, high-density, polyethylene material known commercially as Tyvek®. Created by DuPont, Tyvek® resembles a waxy paper with good whiteness and exceptional strength, maintaining its size and shape with changes in humidity. Tyvek® will not allow dust to be released into the container, is resistant to staining, mold, and mildew growth, and will not reduce adsorption rate. However, because of its special properties, Tyvek® is more expensive than conventional cover stock materials.
CONCLUSION
AGM Container Controls, Inc. has an entire division dedicated to desiccants and their functionality. AGM also offers a moisture analysis service which accounts for a wide range of variables in order to prescribe desiccant combinations for maintaining targeted humidity level goals over any length of time for highly sensitive equipment. If at any time you have questions or concerns, please contact us at 520-391-9103 or via email and we will be happy to assist you.
Summary
What are desiccants?
Manufactured and naturally occurring hygroscopic materials that adsorb moisture from the air in order to protect equipment and items.
What are some common desiccants?
- Silica Gel
- Molecular Sieve
- Montmorillonite Clay
Why are desiccants important?
Moisture damage causes billions of dollars in damage to consumer goods per year and has been the inciting cause of plane wrecks, as well as the failure of electronics and optics equipment throughout various technical industries. As a result, desiccants protect everything from stored household items to NASA equipment.
Do desiccants expire or break down over time?
No, desiccant does not expire and neither do they break down. Rather, desiccant continues to adsorb moisture to a point where it cannot hold any more, in which case it needs to be discarded or regenerated.
Does desiccant have a shelf life?
Desiccant shelf life, when stored in its original protective packaging, is typically 1-5 years. The shelf life depends upon the level of its protective packaging.
What are the optimal store conditions for desiccant?
In its protective packaging, desiccant can be stored in conditions of 0° – 90°F (-17°C – 32°C) at 0% – 75% Relative Humidity (RH). If removed from its protective packaging, desiccant should be placed into use immediately.
How much desiccant do I need?
Use the Desiccant Calculator to quickly estimate how many units of desiccant is appropriate for your application. Otherwise, see MIL-D-3464. For applications requiring a high degree of accuracy in desiccant amounts, contact AGM to discuss your needs.