Molecular sieves adsorb moisture from the air like other desiccants but it is their pore structures and high adsorption capacities that set them apart.
What is molecular sieve and how is it different from other desiccants?
Molecular sieves are adsorptive materials often used as desiccants for the purpose of removing moisture from gases and liquids. They are often made from a type of zeolite, which is a crystalline material with a porous structure that allows for selective adsorption of molecules.
The chemical formula for molecular sieve desiccants is not singular, as there are many different types of molecular sieve materials with varying chemical compositions.
However, molecular sieves are typically composed of metal oxides, such as aluminum oxide, silicon oxide, and titanium oxide, along with other elements, such as sodium, potassium, and calcium.
The specific chemical formula for a particular molecular sieve desiccant will depend on the specific composition of that material, which in turn will depend on the type of molecular sieve and the manufacturing process used to produce it.
Applications
Thanks to their ability to selectively adsorb molecules, molecular sieve desiccants support a wide range of applications in various industries, including:
- Dehydration of gases: Molecular sieve desiccants are widely used for the removal of moisture from gases, such as natural gas, hydrogen, and air, in industries such as petrochemicals, electronics, and food processing.
- Solvent drying: Molecular sieve desiccants can be used to remove water from solvents in the pharmaceutical, fine chemicals, and polymer industries.
- Oxygen enrichment: Certain types of molecular sieve materials can selectively adsorb nitrogen from air, allowing for the enrichment of oxygen for use in medical and industrial applications.
- Refrigerant drying: Molecular sieve desiccants can be used to remove water from refrigerants in air conditioning and refrigeration systems.
- Automotive emissions control: Some molecular sieve materials are used as adsorbents in automotive emissions control systems to capture pollutants such as volatile organic compounds (VOCs) and nitrogen oxides (NOx).
- Industrial catalysts: Molecular sieves can be used as catalysts in a variety of chemical reactions, such as the conversion of methanol to olefins.
The unique properties of molecular sieve desiccants make them an important component in various industrial processes where selective adsorption or catalytic activity is required.
Different Types of Molecular Sieve
There are many different types of molecular sieve desiccants, which differ based on the size and shape of their pores, the specific molecules they are designed to adsorb, and the applications for which they are best suited.
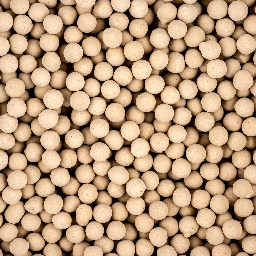
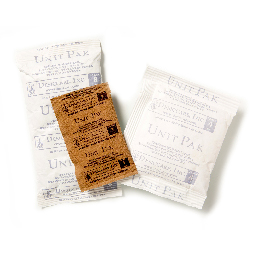
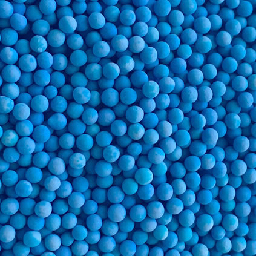
The different sizes of molecular sieves are created by swapping out cations (positive ions) in the chemical makeup of the desiccant. In turn, this creates larger or smaller pores in a highly organized crystalline structure, which enables smaller molecules to pass through while trapping larger molecules. In this way, it’s possible to use molecular sieve to selectively capture specific compounds.
3A, 4A, and 5A molecular sieves are organized in a Linde Type A crystal structure, while the 13X utilizes a Type X crystal structure.
Here are some of the most common types of molecular sieve desiccants:
- Type 3A: This molecular sieve desiccant has a pore size of 3 angstroms and is specifically designed to adsorb water, as well as other polar molecules. It is often used in the petroleum industry for the dehydration of gases and liquids.
- Type 4A: This molecular sieve desiccant has a pore size of 4 angstroms and is designed to adsorb water, carbon dioxide, and other polar molecules. It is commonly used in the natural gas industry for the removal of water and carbon dioxide from gas streams Additionally, it is used in the aerospace industry to reduce the relative humidity in sealed device enclosures, such as aerial cameras. 4A is the sodium cation form of the Linde Type A crystal structure.
- Type 5A: This molecular sieve desiccant has a pore size of 5 angstroms and is designed to adsorb larger molecules, such as water, carbon dioxide, and nitrogen. It is often used in air separation processes, as well as in the production of olefins and other chemicals.
- Type 13X: This molecular sieve desiccant has a pore size of 10 angstroms and is designed to adsorb larger molecules, such as water, carbon dioxide, and nitrogen. It is commonly used in the removal of trace impurities from gas streams, as well as in the drying of air and other gases. 13X is the sodium cation form of the Type X crystal structure.
- Type ZMS: This molecular sieve desiccant has a pore size of 6-8 angstroms and is designed for the selective adsorption of carbon dioxide, hydrogen sulfide, and other acidic gases. It is commonly used in natural gas purification.
- Indicating Molecular Sieve: Similar to blue indicating silica gel, indicating molecular sieve is impregnated with cobalt chloride. Doing so enables the desiccant to change color as it saturates with moisture, providing a clear visual indication of saturation level.
- Packaged Molecular Sieve: Less a type of desiccant and more a delivery method, molecular sieves can also be packaged in small packets rather than purchased in bulk. These packets are preferred for some applications where loose desiccant is unwanted or not ideal.
Additionally, each molecular sieve features different mesh sizes, commonly either 4 x 8 or 8 x 12. Learn more about mesh sizes as it pertains to molecular sieve desiccants.
Be aware that there are many types of molecular sieves and this list is not exhaustive. However, the specific type of molecular sieve desiccant used in a particular application will depend on the specific requirements of that application, such as the type of gas or liquid being dried, the purity requirements, and the desired operating conditions.
How much water can Molecular Sieve adsorb?
The amount of water that a molecular sieve can adsorb before it saturates will depend on various factors such as the pore size of the molecular sieve, the relative humidity of the surrounding environment, and the temperature. Generally, molecular sieves are more effective at adsorbing water than silica gel, often adsorbing approximately 21% of their weight in water and at a faster rate.
Know that it is common industry practice to swap out desiccants once the RH of an enclosure (or other system being desiccated) reaches 40%RH, with the goal of maintaining an RH level less than 40%. Therefore, it is at this level of humidity that most desiccant capacities are compared.
It is also important to note that like silica gel, once a molecular sieve becomes saturated with water, it will no longer be effective at adsorbing moisture. In fact, it may start releasing moisture back into the gas or liquid stream. Therefore, it’s important to monitor the saturation level of the molecular sieve and replace it or regenerate it as needed to ensure that it continues to be effective.
How is Molecular Sieve Made?
Molecular sieve desiccants are manufactured through a series of steps that involve the synthesis of the molecular sieve material, shaping the material into the desired form, and activating it to create a highly adsorptive desiccant. Such processes include:
- Synthesis: The molecular sieve material is synthesized by mixing various chemical components such as alumina, silica, and alkali metal oxides. This mixture is then heated to high temperatures in a furnace to create the desired crystal structure of the molecular sieve.
- Shaping: The molecular sieve material is then shaped into the desired form, such as beads, pellets, or powder. This is usually done by extrusion or spray drying.
- Activation: The shaped molecular sieve material is then activated by heating it to a high temperature in the presence of an inert gas. This process removes any remaining moisture or impurities from the material and creates a highly adsorptive desiccant.
- Packaging: The activated molecular sieve desiccant is then packaged into the desired form, such as bags or canisters, and is ready for use.
It is worth noting that the specific process for manufacturing molecular sieve desiccants may vary depending on the desired application and the specific type of molecular sieve material being used. Additionally, the manufacturing process may include further steps, such as impregnation with certain metals or chemicals, to improve its performance for certain applications.
AGM’s Desiccant Guides
Molecular Sieves compared to other desiccants
Molecular sieve desiccants compared well to both silica gel and activated alumina. Below are some of their benefits:
- Greater Adsorption Capacity: Molecular sieve desiccants have a greater adsorption capacity for water than silica gel or activated alumina up to 40%RH. This means that they can remove more water from the surrounding environment before they become saturated and need to be replaced.
- Selectivity: Due to their crystalline structures, molecular sieve desiccants can selectively adsorb specific types of molecules from the environment.
- Long-Lasting Performance: Molecular sieve desiccants have a longer lifespan than silica gel or activated alumina. This is because they are less prone to surface saturation, which occurs when the desiccant material’s surface becomes coated with moisture and is no longer able to adsorb additional moisture from the surrounding environment.
- Higher Thermal Stability: Molecular sieve desiccants have higher thermal stability than silica gel or activated alumina, which makes them ideal for high-temperature applications. Molecular sieve will retain significant useful capacity at temperatures as high as about 150°C (302°F), while silica gel and activated alumina will lose begin to lose significant capacity above about 50°C (122°F).
While molecular sieve is a highly effective desiccant, its benefit to a given project, as compared to silica gel or activated alumina, will depend on the particular application and its specific requirements. For help choosing, Contact AGM.
How does Molecular Sieve Work?
Like other desiccants, molecular sieves trap moisture (adsorb moisture); effectively removing it from the surrounding atmosphere. However, molecular sieves feature several unique characteristics.
Molecular sieves are formed from zeolite, which provides them with a highly organized crystalline structure. Different sized molecular sieves are formed through the combination of the zeolite with different cations. These two traits (structure and pore size) enable molecular sieve desiccants to adsorb moisture or various other molecules from ambient air, flowing gas streams, and liquids.
How to regenerate molecular sieve
Like many other desiccants, molecular sieve can be regenerated for reuse.
However, due to molecular sieve’s high thermal stability, regenerating temperatures are in the range of 400°C (752°F) to 600°C (1112°F), in order to remove adsorbed water and other impurities. This range is much higher in comparison to silica gel or activated alumina.
The exact regeneration process can vary depending on the specific molecular sieve material and its intended application, but it typically involves heating the desiccant material in a stream of hot gas, such as nitrogen or air, for a period of time.
Optimal Storage Conditions of Molecular Sieve
AGM recommends storing molecular sieve in metal cans at room temperature (between15°C (60°F) and 27°C (80°F)) with humidity between 0%RH and 70%RH.
How long does molecular sieve last
AGM guarantees its molecular sieves for a minimum 1-year shelf life when stored in the original, unopened packaging.
How much do I need?
AGM is developing a sweet of tools to help you determine how much desiccant is necessary to protect your project. AGM’s Desiccant Unit Calculator is a free tool that provides desiccant unit quantities for Molecular Sieve, Silica Gel, and Clay desiccants based on a given volume of space.
Conclusion
Molecular sieve desiccants play a significant role in the moisture protection process for a wide set of industries. Their strengths include high adsorption capacity, great thermal stability, and selectivity of molecule capture.
Have other questions and want to find the answers yourself? See AGM’s Desiccant FAQ. If you can’t find what you’re looking for, email us or give us a call at (520) 881-2130.