Breather Valves (also known as Pressure Relief Valves)
AGM breather valves are designed to manage pressure and vacuum differentials among sealed containers, enclosures, housing – any sealed space. Stopping pressure and vacuum from exceeding an enclosure rating protects the enclosure and the equipment inside.
- Container Access
- Corrosion Prevention
- Humidity Monitoring
- Moisture Control
- Moisture Purging
- Pressure Control
- Shelving & Straps
- Shock Monitoring
Find What You're Looking For
It’s a lot, we know. If you’re looking for something specific or aren’t sure what you need, try searching through all products or give us a shout and we’ll help!
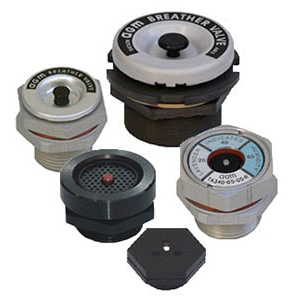
What is a Breather Valve?
What is a breather valve, exactly? A breather valve, also known as a pressure relief valve, prevents excessive pressure or vacuum buildup in a sealed container, enclosure, or other sealed space.
AGM carries two variations of breather valves in a variety of sizes:
- Spring-actuated breather valves
- Effective in most circumstances.
- Magnetically-actuated breather valves
- Effective for decompression and rapid differential relief.
How Do Breather Valves Work?
Breather valves automatically adjust the internal pressure of a sealed space with respect to the ambient pressure. This stops excessive differentials from damaging containers, housing, or enclosures.
Spring-actuated breather valves are common in most pressure mitigation systems. This type of breather valve is factory set at a specific cracking pressure (also known as an opening pressure) and will open once pressures reach that threshold. Spring breather valves operate via a poppet and spring method, whereby a spring at tension maintains the poppet in a closed position. Once the pressure reaches the cracking point, the spring tension is overcome, the poppet is pushed in, and the air is allowed to flow through the valve to relieve either pressure or vacuum.
Magnetically-actuated breather valves are most effective in circumstances involving pressure differentials of great magnitude with high rates of change, such as decompression events or when the rate of pressure change is too great for a spring breather valve to safely handle. Magnet breather valves function very similar to spring breather valves except that magnets are used in place of springs. The magnets enable these valves to fully open near instantaneously and provide a greater amount of air flow faster.
What Are Pressure Differentials
Pressure differentials are an inherent challenge in the aerospace industry. As an aircraft or spacecraft ascends to higher altitudes, the air pressure outside the vehicle decreases while the pressure inside remains constant. This is also the case for externally mounted equipment, such as aerial optics systems or electronics housings.
The difference in pressures is known as a pressure differential, and it can lead to problems such as leaks, material failure, and even structural damage, if not managed properly. Under most conditions, pressure differentials are generated slowly and may be relieved with common spring breather valves. However, under some conditions, such as rapid ascent, descent, or rapid decompression, spring breather valves may not be enough. In such cases, ultra high flow breather valves, or magnet valves, can provide a great deal more air flow faster.
However, aerospace engineers need to understand both the rate of change and magnitude of pressure differentials that occur during flight to properly protect craft and equipment.
Breather Valves and the Rate of Change of Pressure Differentials
As an aircraft or spacecraft ascends, a pressure differential can develop quickly. If pressure is not equalized to safe levels fast enough, a differential in excess of a vehicle or enclosure’s pressure rating may develop. As a result, such excessive pressures can cause catastrophic failure of the vehicle or equipment.
As a point of emphasis, the rate of change is of special concern in comparison to the magnitude when specifying breather valves. This is because a breather valve, to be effective, will have to flow enough air at a fast enough rate to avoid the development of a magnitude greater than the given enclosure’s pressure rating.
Therefore, when reviewing breather valves, it’s very important to know the rate of change in pressure differential that the enclosure in question will experience.
Breather Valves and the Magnitude of Pressure Differentials
Nevertheless, the magnitude of a differential is important in determining an appropriate breather valve for a given situation.
First and foremost, it’s important to review the pressure/vacuum rating of a given enclosure, as this will provide the maximum differential allowable.
Once the maximum pressure differential has been determined, the flow capability of a given breather valve is evaluated at that maximum pressure. Doing so provides a determination as to whether the flow through the breather valve is sufficient to protect the enclosure.
Managing Pressure Differentials During Flight, Altitude Change, or Temperature Cycling
Breather valves prevent damage through the equalization of pressures to safe operating levels.
To do so, a breather valve must sufficiently relieve pressures within a time interval that would otherwise see the development of a pressure differential greater than an enclosure’s pressure rating. For example, during a decompression event, a breather valve must be able to open quickly enough and to provide enough flow as to prevent damage, such as ruptured seals or deforming enclosure walls.
Rockets, planes, and spacecraft all ascend and descend very quickly. During their flight, the ascent and descent speeds may be great enough to generate differentials both in significant magnitude and rate that can easily cause damage to an enclosure and see a breather valve struggle to keep up if not appropriately planned.
For this reason, it’s very important to have a firm understanding of cracking and reseal pressures, how pressure differential rate and magnitude factor into a breather valve’s performance, and the difference between spring and magnet breather valves.
Breather Valves for Aero and Others
It is worth noting that while the core technology and function of the breather valves discussed above are the same as those common to other industries – such as chemical storage – certain aspects may differ in important ways.
In the aerospace industry, breather valves are used to manage pressure and prevent damage to sensitive electronic components, ensure proper fuel flow, and control internal pressures, such as in the cabin of an aircraft. Frequently, they are also used on transport containers, cases and device enclosures shipped via truck, aircraft, or ocean vessel. These breather valves are designed to withstand the extreme temperatures, pressures, and environmental conditions that are frequently encountered during flight and shipping.
Conversely, breather valves used in an industry such as chemical storage, are primarily used to regulate pressure, and prevent the buildup of hazardous gases in tanks. These valves help to maintain a safe environment for workers and prevent explosions or other accidents that can result from the buildup of pressure or flammable gases. Such breather valves are typically designed to withstand exposure to harsh chemicals, corrosive substances, and other hazardous materials.
Types of Breather Valves
AGM carries mainly two types of breather valves used in aerospace applications: spring-actuated and magnetically-actuated valves. Both types of valves perform the same function of regulating pressure differentials, but they do so using different mechanisms. These variations in their functioning make each type of breather valve better suited to different situations.
Spring Breather Valves
Spring-actuated breather valves use a spring to regulate the valve opening.
A spring breather valve consists of a:
- Valve body,
- Spring; and,
- Disc or poppet that seals the valve.
As pressure increases above the set point of the valve, the spring compresses, causing the poppet to lift off its seal. This pressure level is known as cracking pressure and is the point where the valve opens to allow air to pass through.
As pressure further increases, the valve gradually opens with it, eventually reaching a maximum and allowing its greatest possible air flow to equalize the differential.
As the pressure differential is reduced to a safe level, the spring decompresses, causing the disc or poppet to return to its original position and the valve reseals.
Spring breather valves are simple, reliable, and low cost, but the gradual increase in air flow from cracking to full flow makes them less suited for situations in which a great deal of air must flow in a short period of time.
Magnet Valves (Ultra-High Flow Breather Valves)
Magnetically-actuated breather valves use the attractive force between two magnets to control the valve opening.
A magnet breather valve consists of a:
- Valve body,
- Diaphragm,
- Retention spring; and,
- Magnet pair.
As pressure increases above the set point of the valve, one of the magnets is pushed back. Once the distance between the two magnets has increased beyond a certain point, the attractive force is not strong enough to hold them and the valve flies fully open to allow full-flow pressure relief almost instantaneously.
As the pressure differential is reduced to a safe level, the retention spring provides just enough force to push the magnet back into a distance with the other magnet wherein their attractive forces hold them closed.
Magnet valves provide greater air flow faster in comparison to most spring valves and can regulate a wider range of pressure differentials.
Magnet Breather Valves for Rapid Decompression Relief
AGM magnet breather valves are designed for relieving pressure differentials during rapid decompression events.
How to Choose the Right Breather Valve
Before making a definitive choice, you’ll need to know:
- How much pressure or vacuum your enclosure or container can withstand
- The internal air volume of your container or enclosure
- The expected rate of change of pressure
- The tolerance of the contents for moisture and particulate
To choose an appropriate breather valve, it’s important to understand that, fundamentally, a breather valve must perform two functions: Protect a container from excessive pressure or vacuum differentials, while limiting the amount of moisture that enters the container. Therefore, an ideal valve should remain sealed except during altitude change or under extreme temperature changes, but when open should provide sufficient flow to relieve air pressure as fast as it builds up.
It should be noted that breather valves set as low as +0.5 (pressure) and -0.5 (vacuum) psid will protect against excessive moisture intrusion for years.
Use our Breather Valve Selection Chart below for the flow rates of the various breather valves we carry.
Valve Series Part Number | Flow Rate | Maximum Net Volume of Container |
---|---|---|
TA292-R | 0.5 scfm† | up to 4 cu.ft.‡ |
TA294-R | 1.0 scfm† | up to 8 cu.ft.‡ |
TA340-R | 0.5-3.0 scfm*† | up to 25 cu.ft.‡ |
TA238 | 4.0 scfm† | up to 33 cu.ft.‡ |
TA240-R | 4.0 scfmt | up to 33 cu.ft.‡ |
TA330 | 1.5 - 4.0 scfm*† | up to 33 cu.ft.‡ |
TA333-R | 1.5-4.0 scfm*† | up to 33 cu.ft.‡ |
TA440-R | 2.0-4.0 scfm*† | up to 33 cu.ft.‡ |
TA770-R | 10 - 25 scfm*† | up to 208 cu.ft.‡ |
TA761-P | 40- 140 scfm*† | up to 1167 cu.ft.‡ |
TA762-V | 40- 140 scfm*† | up to 1167 cu.ft.‡ |
TA796-P | 170-800 scfm*† | up to 6667 cu.ft.‡ |
TA797 | 525 scfm | up to 4375 cu.ft.‡ |
TA798-V | 280 - 600 scm*† | up to 5000 cu.ft.‡ |
* Depends upon relief setting of valve. † To convert to metric equivalent (liters/sec) multiply br 0.472 ‡ To convert to metric equivalent (m3) multiply br 2.831 x 102 |
When choosing between spring-actuated and magnetically-actuated valves, aerospace engineers must account for many performance factors, including:
- Pressure range
- Response time
- Accuracy
- Reliability
…and much more! These factors can vary depending on the specific application and operating environment.
This process requires careful consideration and is often best done in collaboration with experienced professionals.
For technical assistance in selecting a breather valve for your application, contact AGM.
Specifications & Requirements
AGM breather valves are rigorously tested to ensure that they meet or exceed appropriate industry and government standards.
SAE Specification AS27166, entitled “Valve: Pressure Equalizing, Gaseous Products,” details environmental requirements and the procedures for vibration, temperature, salt, fog, sand and dust, rough handling, etc., as well as settings and flow. (Note: Many design activities have found it impractical to use the settings designated in this specification and have called out other settings more suitable for their particular container design.)
IMPORTANT: AGM Breather Valve Series TA238, TA240-R, TA330, TA333-R and TA770-R will meet all requirements of this specification (see Environmental Protection, above). AS27166 is also referenced in Department of Defense MIL-STD-648C.
Additionally, every AGM breather valve is individually tested and certified for compliance with performance requirements.
If you require identification of an AGM breather valve with a part number other than one shown on this website, please contact us for part number verification. Let us know if you also plan to put one of AGM’s catalog numbers on a document requiring MIL-STD-130 identification.
Mounting and Installation
Unless otherwise specified, all AGM breather valves are supplied with a nut, washer and gasket for
Unless otherwise specified, all AGM breather valves are supplied with a nut, washer and gasket for mounting through a hole on a flat, smooth surface. Valve gaskets may not provide a proper seal if the mounting surface is curved or rough. AGM breather valves can also be installed in a mounting flange or a threaded boss when a suitable counter bore has been provided for thread relief.
Additional Features
Some breather valves may come with or have the option to include:
- Manual release buttons: Push to release internal pressure or vacuum. This is especially desirable for containers with large lids or robust seals.
- Weather shielding: Weather shields help to prevent liquid water and debris from entering an enclosure when the breather valve inhales.
- Built-in humidity indication: Option for a humidity indicator card on the face of the valve. This enables quick visual inspection of the humidity level inside of an enclosure.
Looking for something more custom?
If you have special requirements which cannot be met by using a standard valve, please contact our design engineering team regarding possible modifications or a special valve design to meet your needs.
How Breather Valves Protect
How a breather valve protects contents in a container from moisture intrusion depends on five factors:
1. Pressure and Vacuum Settings
Breather valves are made in a variety of settings (points when the valve seals), ranging from 0.2 psid to 5.0 psid or more. These settings must be at least 1.0 psi to 1.5 psi below the pressure or vacuum. The lower the valve setting, the more often the valve will open, admitting outside atmosphere and shortening the life of any internal desiccant used to capture moisture.
2. Temperature Variations
The number of times a breather valve will open during storage depends not only on the valve setting but on the magnitude and frequency of temperature variations that occur.
3. Temperature Vs. Humidity
In addition to the number of times the breather valve opens, the amount of moisture taken into the container at each opening will determine desiccant life (dependent on climate conditions of the storage area)
4. Number of Airlifts
If the enclosure is experience flight, the amount of desiccant needed will depend on the number of airlifts anticipated.
For every descent from 10.7 psia (normal pressurization level in an aircraft cargo compartment) to 14.7 psia (sea level), a breather valve set for 0.5 psid reseal in both directions will take in 0.055 grams of water per cubic foot of container volume.
5. Amount of Desiccant
A Breather Valve, properly selected and used in conjunction with adequate desiccant, can provide years of moisture protection in a lightweight, low-cost container.
Breather Valve Applications
We specialize in aerospace, defense, and logistics applications. Here are a few containers that currently use our breather valves:
1. M6 Rifle Container (using the TA333-R Valve)
2. Single Missile Container (using the TA333-R Valve)
3. Personnel Carrier Engine / Transmission Container (using the TA330 Valve)
4. Transit Case (using the TA333-R Valve)
5. F100 Engine Container (using the TA770-R Valves)
6. Phoenix Missile Container (using the TA440-R Valve)
Frequently Asked Questions
Sometimes we’re asked to supply a valve that will “crack” (start to open) at a specified pressure, within a tolerance. While this requirement can be met, it involves additional testing, increased cost, and (except under extraordinary circumstances) is often unnecessary, since the settings for seal and design flow provide the desired protection for both container and contents.
In addition, SAE Specification AS27166 sets maximum cracking pressure offsets from the reseal pressure.
Yes, SAE Specification AS27166 requires that breather valves must still reseal after being tested for sand and dust protection per MIL-STD-810.
The sand used in the test is similar to talcum powder, too fine to affect the sealing surfaces of the valve. However, the specification does not require the valve to keep sand and dust out of the container if it opens during a dust storm. This technicality has made it possible for valves with stamped or wire mesh screens to certify as meeting the specification.
For total sand and dust protection, you would choose the following AMG breather valve series: TA330, TA333-R or TA770-R. These valves have dust baffles and covers that will protect the contents of the container from not only sand and dust but also wind-driven rain and water from high-pressure decontamination hoses.
Yes, our breather valves work automatically, but valves with a manual release button can also be opened manually to equalize pressure.
No, these breather valves do not completely equalize the pressure between the interior and exterior of the container, unless you push the manual release button (if applicable). In automatic mode, they will equalize only to the level of the reseal pressure.
It depends. There are three common ways that liquid water can enter through a breather valve: submersion in water, directed streams of water (washdowns), and wind-driven rain.
For submersion, the valve will not open if the reseal pressure of the valve exceeds the .hydrostatic pressure of the water plus any vacuum that has built up inside the container. Submerging a warm container in cold water will develop a vacuum inside the container. If your container is subject to this condition, contact us for assistance in calculating its effect on your container.
For washdown, the breather valve’s cover configuration and vacuum setting determine whether it is susceptible to water ingress. Our AGM breather valves with a solid cover and a nominal cracking pressure in the vacuum direction of at least 1.0 psid will repel water entry from a directed stream of water. AGM valves with a solid cover include the following: TA333-R, TA330, TA770-R, and TA225.
Finally, for the condition of wind-driven rain, our AGM breather valves with a solid cover will repel wind-driven rain even when the valve is inhaling. AGM’s unique cover design forces the airstream through two 180° turns, thereby causing most water droplets to fall out of the air stream.
Note that the passage of liquid water through a valve is only one way moisture can enter a container. The more common way for moisture to enter a container is in the form of water vapor. Contact us for assistance in determining how to protect your container’s contents against this type of water ingress.
No, our AGM breather valves are small mechanical systems where a spring pushes a seal onto a seat. Due to the surface energy forces of the elastomeric seals, it will always require slightly more force to open the valve than to close it. Therefore, the opening pressure will be slightly higher than the reseal pressure. The higher the setting of the valve, the greater the difference between the opening and closing pressures.
We have made valves with reseal pressures as high as 10 psid. However, these valves are difficult to work with and the settings may shift after long periods of time and large temperature changes.
Yes, our breather valves do resist liquid water and debris. However, some water vapor ingress does occur when the valve opens. Please note that careful attention paid to the cracking and resealing pressures is important in ensuring that liquid water does not enter an enclosure during the breather valve’s functioning, as well as minimizing water vapor ingress.
Yes, many of our breather valves feature manual release buttons. Be sure to inquire about the manual release when ordering as not all models come standard with manual release buttons.
No, our breather valves don’t completely equalize the pressure between the interior and exterior of the enclosure.
During automatic actuation, a breather valve will equalize only to the level of the reseal pressure. For example, if a breather valve has a reseal pressure of 0.5 psid, then the pressure will only be equalized to within 0.5 psid because below that pressure, the valve will be closed. However, full equalization may be achieved with the use of a manual release button, on the breather valve models that feature manual release buttons.
Can't find what you're looking for?
We’re here to help. Easily find a product using our onsite search feature or get in touch with any questions!