Summary
Aerial optics systems are under constant development in the aerospace industry and they come with their own set of challenges. For example, the challenge in mitigating the pressure differential on a device housing as it increases and decreases in altitude is often compounded by lens and electronic sensitivities to contaminates, such as moisture and particulate. As a result, addressing the additional parameters normally restricts any one solution to mitigating pressure differentials.
An engineer at a global aerospace firm asked AGM to design and manufacture a custom breathing desiccator to safeguard their product given challenging circumstances, including:
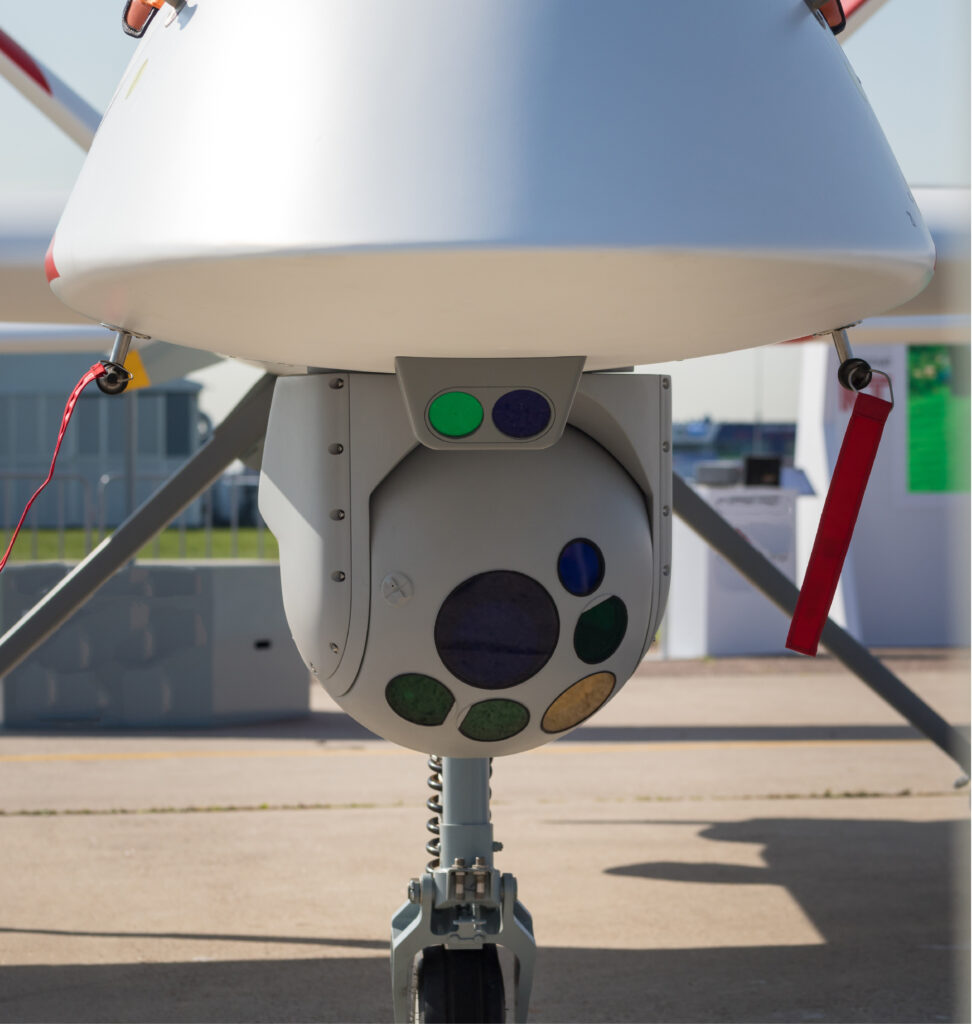
- Rapid ascent and descent velocities
- Greater than standard maximum altitude
- Components with heightened sensitivity to moisture and particulate
- Very small device housing with little free internal volume
The Problem
Certain aspects of the project were subject to common issues. For example, optics assemblies rely predominately on lenses and electronics, which have inherent sensitivities to moisture and particulate. Lenses can fog or be scratched, obscuring or fully preventing any ability for the optics to acquire clear images. Furthermore, electronics can corrode and short-circuit, making any functionality impossible.
However, the components used in this particular project featured acute sensitivities to both moisture and particulate contamination. Additionally, the rates at which pressure differentials are generated in the device housing are very fast. If pressures are not relieved quickly, the enclosure can deform, rip, and pop – destroying the device.
The Solution
How We Solved the Pressure Differential:
The pressure differential required a breather valve to be installed in the device enclosure.
While the magnitude of the differential wasn’t an issue, the rate at which it developed required a great deal of air flow, which was a challenge given several other conditions discussed further below.
In an ideal situation, a large, high-flow breather valve would be installed to safely dispel the pressure differential. However, the enclosure simply didn’t provide enough space for a large valve.
As a compromise, a smaller breather valve was chosen with the understanding that several would have to be installed in order to achieve the necessary air-flow rate.
How We Solved the Moisture Sensitivity:
The component sensitivity to moisture required the enclosure’s internal relative humidity (RH) be kept very low. This demand dictated the use of desiccant.
Further, in order to dry incoming air before it contacts device components, the desiccant is stored in a cannister attached to the rear of the breather valve. However, the desiccant and cannister assembly does reduce the flow rate through the breather valve. This reduction had to be compensated for through the breather valve model, its settings, and the total number installed.
How We Solved the Particulate Sensitivity:
The component sensitivity to particulate required strict filtration.
To provide an adequate level of filtration, AGM engineers decided that a membrane filter was necessary. The filter would come to be installed at the end of the cannister containing the desiccant. However, the pore size of the membrane filter reduced air flow to approximately 25% of full capacity. Such a reduction again prompted reassessment of the total number of assemblies installed in the device housing.
The Final Assembly
As a result, the final assembly designed by AGM consisted of a breather valve, an attached desiccant cannister, a membrane filter, and bagged desiccant. Several of these assemblies were required per device in order to achieve adequate air-flow to dispel dangerous pressure differentials.
The base individual products making up each assembly include:
In the end, the final assembly is a variation on AGM’s cartridge-styled breathing desiccators.
Conclusion
Over a period of months, AGM Design Engineers worked with our customer to successfully develop a custom-made product to ensure the safety of their project and investment.
Additionally, AGM was able to hit target deadlines to ensure the customer’s project remained on course.
These efforts were aided with the help of AGM’s proprietary software. Due to the significant travel speeds of the device, several specialized programs were required in the design process to determine with a high degree of accuracy the hardware requirements for full protection. This software was developed by AGM for analysis of complex and sensitive scenarios such as that described here. The software is not available commercially.
About AGM
Since 1970, AGM Container Controls Inc. has worked with leaders in the Aerospace & Defense industry and U.S. government to ensure the safety and operation of some of the world’s greatest innovations. From land-based defense systems to satellites in space, AGM keeps you safe.