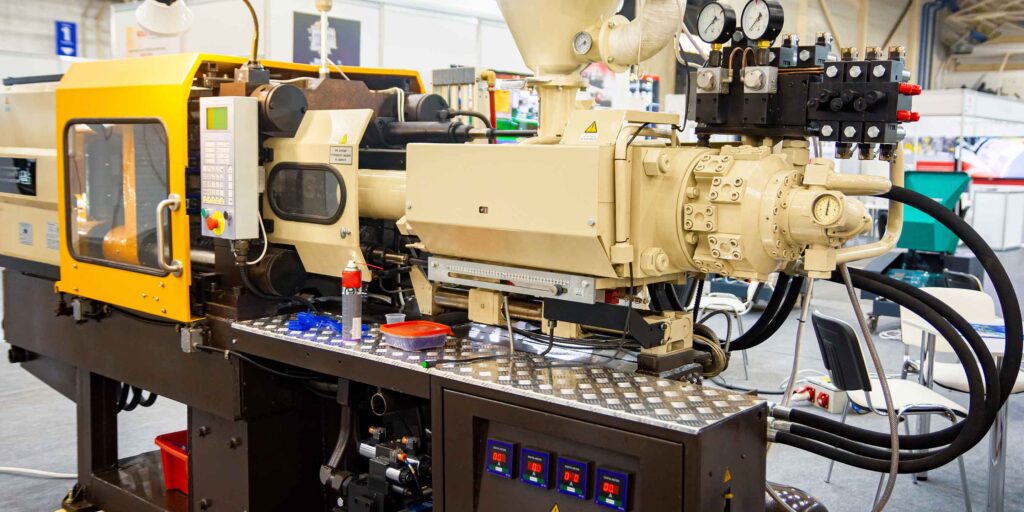
Better Moisture Adsorption with Injection Molded Desiccants
Interested in a Sample?
Want to see it for yourself? Click Get a Sample! and tell us where to send it!
Have a question? Click the Contact Us button and ask us anything!
Injection molding offers many benefits already well known to engineers and manufacturers, including:
- Low Cost Per Part
- Repeatability
- High Detail and Complexity
- Component Strength
Perhaps less well known is how these same benefits provide a unique opportunity to the manufacture of custom molded desiccants.
Injection molding offers many benefits already well known to engineers and manufacturers, including, low cost per part, repeatability, high detail and complexity, component strength. Perhaps less well known is how these same benefits provide a unique opportunity to the manufacture of custom molded desiccants.
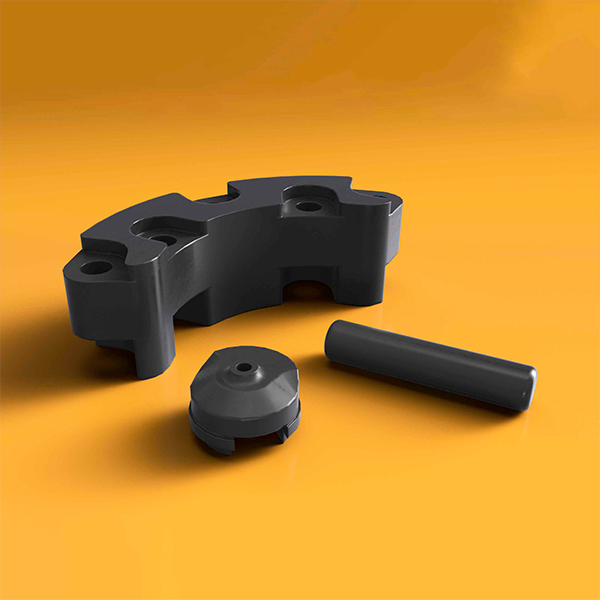
Injection Molding Benefits to Custom Molded Desiccants
Typical of injection molding, dies are created to precise specifications for a given application. The material, which consists of 4A molecular sieve desiccants and polymer binders, are then sent through the injection molding machine and formed in the die.
Injection molding enables large scale production of precision-fit desiccants that feature the adsorption properties of molecular sieve. Further, moisture adsorption is maximized as a result of the desiccant occupying the full volume of space specified.
The injection molding process enables desiccants to provide moisture adsorption in nearly any enclosed volume, regardless of the volume’s shape complexity, and are tough enough for use as structural components. Further, such parts may be made at scale with great precision and at low cost, which produces desiccants better suited to the moisture protection needs of technical industries.
Challenges in Providing Moisture Protection
Moisture protection can become a challenge across many industries. Often, the difficulty in desiccating equipment is brought about through constraints in available space and complexity within an object’s enclosure, as well as the environment in which the object is stored or used.
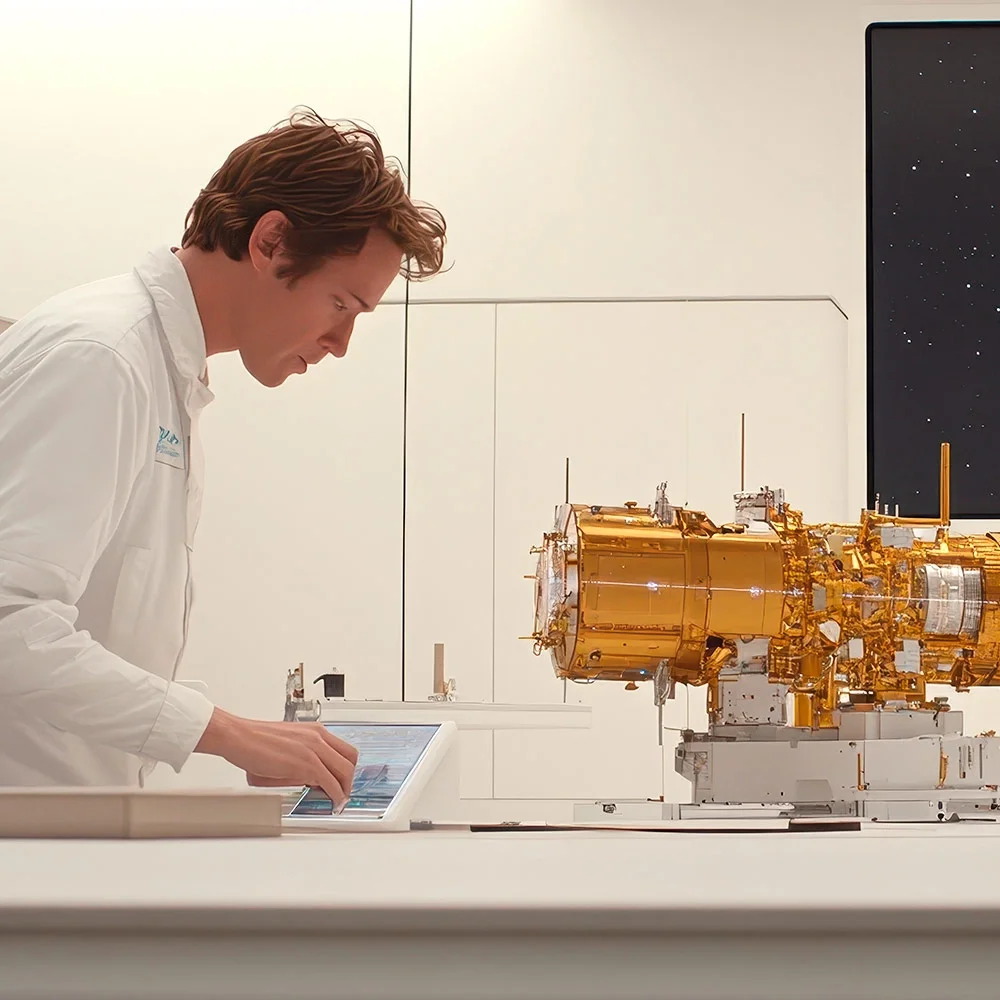
Who Benefits from Injection Molded Desiccants?
Generally speaking, technical industry companies or anyone developing mechanical or electrical products with limited free space but a need for robust moisture protection.
For example, cameras used on drones require moisture protection to prevent lens fogging and electrical corrosion, but any available space inside the housing is both limited and geometrically complex. Furthermore, standard bulk or packaged desiccants pose their own challenges in that they require engineers to include some additional method for securing them and introduces the risk of loose desiccant throughout the camera.
Like a drone camera, there exist many situations in which standard desiccants are not the best solution, such as test, measurement, and monitoring instrumentation. However, for all such situations, molded desiccants offer a solution.
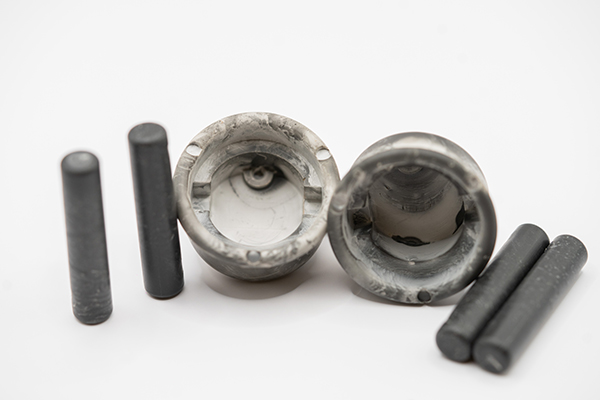
Molded Desiccants and Injection Molding
Molded desiccants are created through injection molding. As such, they are built to tight tolerances and are formed to fit complex geometries and small spaces.
This means that a molded desiccant can fill up to 100% of available internal space – providing more desiccant per volume compared to other solutions – and is strong enough to be used as a design component, if desired.
Finally, the injection molding process allows for repeatable, low-cost production in a variety of quantity demands. Therefore, by leveraging the advantages of injection molding, it’s possible to create a desiccant that meets moisture protection demands while providing design simplification and cost saving to the project.
AGM’s H2OLock Molded Desiccants Provides
Low Cost Per Part
Once the mold is created for a specific job, tens of thousands to hundreds of thousands of parts may be produced. As a result, the cost per part can be very low. This is the case with AGM’s molded desiccants, making them a cost-effective option for those requiring a custom, high performance desiccant.
Repeatability & Precision
Injection molding utilizes a parts mold to create detailed pieces held to tight tolerances. Molten material is injected into the mold and held at high pressure to produce virtually identical parts. This is valuable for creating precision custom desiccants such as H2OLock molded desiccants. Such pieces may be geometrically complex to fit available volumes without compromising a design.
Component Strength
Due to the molecular composition of thermoplastics in combination with the pressure with which they are forced into the parts mold, injection molded pieces are densely packed. As a result, injection molded plastics can feature greater strength in comparison to others. In regard to H2OLock Molded Desiccants, it is this strength that enables the desiccants possible use as a structural component. Furthermore, the desiccant may be epoxied to PCB boards and the like, or secured with screws.
Fit Desiccants into Your Project
Want to see it for yourself? Click Get a Sample! and tell us where to send it!
Have a question? Click the Contact Us button and ask us anything!